Dieser Artikel nennt die sieben häufigsten Fehler beim Risikomanagement, auf welche das Johner Institut und seine Auditoren am häufigsten stoßen. Er gibt auch Tipp dazu, wie sich diese Fehler vermeiden lassen.
Das Risikomanagement zählt zu den wichtigsten Anforderungen, die Medizinproduktehersteller erfüllen müssen. Deshalb ist es wichtig, dass sie Fehler beim Risikomanagement vermeiden.
Nutzen Sie die Punkte in diesem Artikel als Checkliste für Ihre Risikomanagementakte!
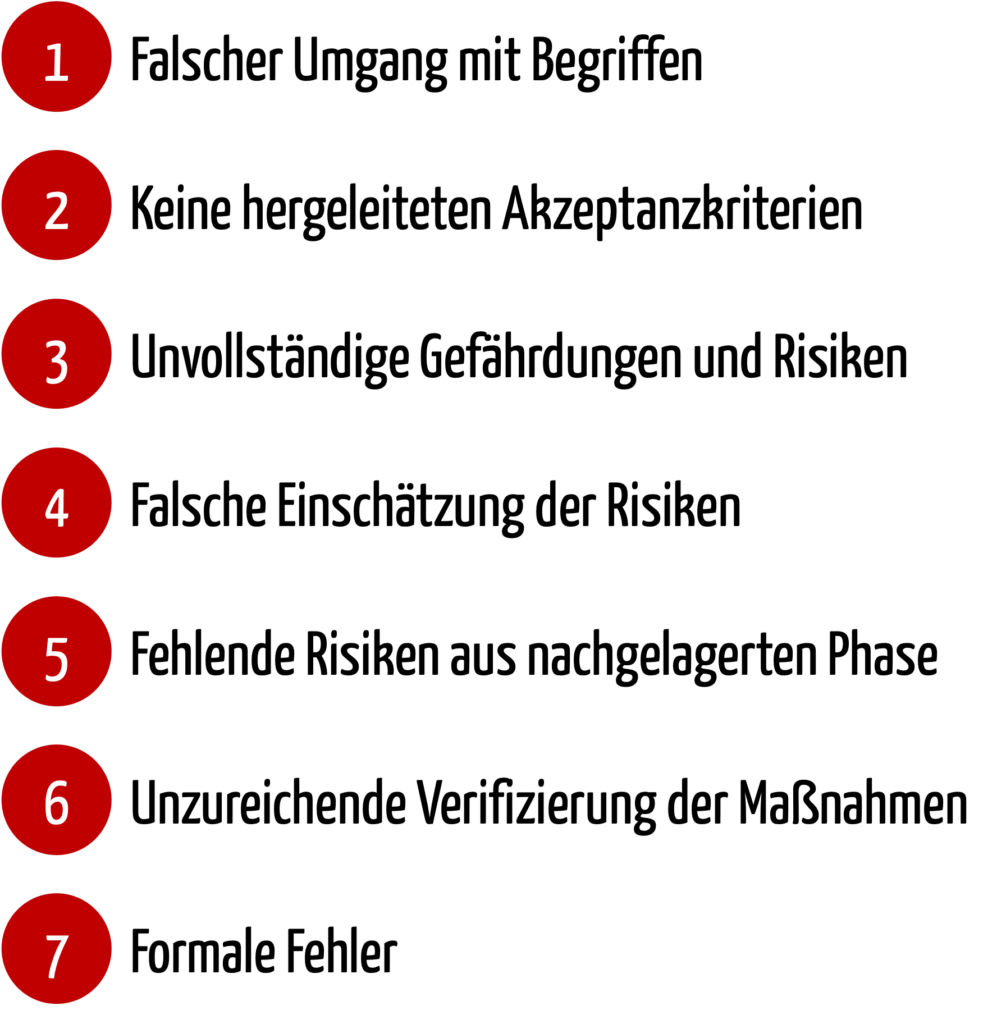
1. Fehlerklasse: Falscher Umgang mit Begrifflichkeiten
Die ISO 14971 definiert die relevanten Begriffe wie Schaden, Gefährdung, Gefährdungssituation, Risiko und Schweregrad. Hierbei unterlaufen den Herstellern regelmäßig Fehler:
- Eine Fehlfunktion eines Geräts wird als Gefährdungssituation bezeichnet, obwohl es eine Gefährdung wäre.
- Die Spalte „Risiko“ enthält Einträge wie „elektrische Energie“, obwohl diese die Gefährdung darstellt.
- Der Hersteller listet den Strahlenschaden bei den Gefährdungen auf, obwohl das ein Schaden ist.
Es fehlt meist auch ein gemeinsames Verständnis im Unternehmen, welches Element der Ursachenkette in die Gefährdungsspalte eingetragen werden soll.
Besonders heikel wird es, wenn Hersteller die Risiken als das Produkt von Wahrscheinlichkeit und Schweregrad möglicher Schäden berechnen. Das ist weder mathematisch sinnvoll noch konform mit der Definition des Begriffs Risiko.
Die Risikoprioritätszahl, also eine Größe von drei Faktoren, von denen eine die Erkennbarkeit ist, entspricht nicht dem Risiko im Sinne der ISO 14971.
Lesen Sie im Artikel über die Risikoprioritätszahl, wann Hersteller diese Größe dennoch verwenden dürfen.
2. Fehlerklasse: Keine systematisch hergeleiteten Akzeptanzkriterien
Die Risikoakzeptanzkriterien müssen die Hersteller für jedes Produkt herleiten. Es ist somit (fast immer) ein Fehler beim Risikomanagement, die Risikoakzeptanzmatrix global in einer SOP zu definieren.
Die Risikoakzeptanzkriterien sollten die Hersteller auch nicht schätzen, sondern möglichst mathematisch herleiten. Dabei sollten sie einen weiteren Fehler vermeiden:
Sie sollten in der klinischen Bewertung nicht einen anderen Nutzen quantitativ und qualitativ nachgewiesen haben, als er Verwendung findet bei der Abwägung des Nutzen-Risiko-Verhältnisses und damit bei der Herleitung der Akzeptanzkriterien.
Eine Voraussetzung, dass die Hersteller die Akzeptanzkriterien in Form einer Risikoakzeptanzmatrix zum Ausdruck bringen besteht darin, dass die Achsen präzise definiert sind. Beliebte Fehler dabei sind:
- Die Ereignisse in der Wahrscheinlichkeitsklasse „unvorstellbar“ treten rechnerisch bei allen Anwendungen bei allen Produkten über die komplette Lebenszeit hundert- oder gar tausendfach auf und sind damit alles andere als „unvorstellbar“.
- Die Schadensklassen sind nicht präzise mit Hilfe von binären Entscheidungsmerkmalen definiert.
Der Artikel zur Risikobewertungsmatrix gibt Ihnen konkrete Hinweise dazu, wie Sie eine solche Matrix normenkonform und produktspezifisch festlegen.
3. Fehlerklasse: Unvollständige Gefährdungen und Risiken
Der nächste Typ an Fehlern beim Risikomanagement betrifft die Vollständigkeit der identifizierten Gefährdungen und damit Risiken. Die Gründe für die Vollständigkeit sind mannigfaltig:
- Der Hersteller hat die Methoden zur Gefährdungsanalyse nicht oder nicht präzise angewendet.
- Die Fehlerfolgen, die er mit der Design-FMEA oder Prozess-FMEA identifiziert hat, erscheinen nicht als Gefährdungen in der „Risikotabelle“.
- Die Risiken durch mangelnde Gebrauchstauglichkeit wurden nicht systematisch ermittelt, beispielsweise weil Usability Tests nicht oder nicht mit repräsentativen Nutzern und nicht in repräsentativen Nutzungsumgebungen durchgeführt wurden.
- Der Hersteller betrachtet die Gefährdungen erst nach den Maßnahmen z.B. nachdem er ein zweikanaliges Design gewählt hat. Das wäre nicht konform und würde nicht sicherstellen, dass zu diesen Gefährdungen die Maßnahmen auch weiterhin auf Wirksamkeit geprüft werden.
Weiterführende Informationen
Weitere Artikel helfen Ihnen, genau diese Fehler beim Risikomanagement zu vermeiden:
4. Fehlerklasse: Risiken falsch eingeschätzt
Das nächste Fehler beim Risikomanagement besteht darin, dass die Hersteller die Wahrscheinlichkeiten und Schweregrade von Schäden falsch einschätzen. Das hat wiederum mehrere Ursachen:
- Die Abschätzung ist per se schwierig.
- Der Hersteller hat nicht die ganze Ursachenkette betrachtet. Ihm fehlen somit die Informationen, die für die Abschätzungen notwendig sind.
- Das Personal verfügt nicht über die notwendige Kompetenz. Beispielsweise kann nur eine Ärztin oder ein Arzt die Wahrscheinlichkeiten und Schwergrade abschätzen, die sich bei einer gegebenen Gefährdungssituation ergeben.
Viele Hersteller tendieren dazu, immer nur den Worst-Case (Tod) zu untersuchen. Es ist aber ein Fehler zu vermuten, dass das größte Risiko immer bei den größten Schweregraden vorliegt.
5. Fehlerklasse: Risiken aus der nachgelagerten Phase übersehen
Doch selbst mit der besten Methode und den größten Expertinnen und Experten, sind die in den Abschnitten drei und vier genannten Fehler in den Risikomanagementakten nicht zu vermeiden.
Daher ist es unerlässlich, kontinuierlich Informationen aus nachgelagerten Phasen wie der Post-Market Surveillance zu sammeln und damit die Risikoanalyse zu ergänzen und zu verbessern.
Ein weiterer Grund ist der sich ändernde Stand der Technik, den die Risikoakzeptanzkriterien widerspiegeln müssen.
Die nachgelagert Phase im Sinne der ISO 14971 beinhaltet auch die Produktion. Regelmäßig vergessen Hersteller, die durch die Produktion verursachten Risiken zu analysieren. Bei jeder Änderung der Produktion müssen die Hersteller diese Analyse aktualisieren. Genau das unterbleibt aber oft, was einen weiteren Fehler im Risikomanagement bedeutet.
6. Fehlerklasse: Keine ausreichende Verifizierung der Maßnahmen
Eine weitere Fehlerklasse betrifft die Verifizierung der Maßnahmen. Entweder diese Verifizierung unterbleibt bei einzelnen Maßnahmen ganz. Oder die Hersteller sind sich nicht bewusst, dass zwei Verifizierung notwendig sind:
- Verifizierung, dass die Maßnahme ungesetzt wurde, z.B. durch ein Review des Produkt-Entwurfs
- Verifizierung der Wirksamkeit der Maßnahmen, typischerweise durch entsprechende Tests
Es gibt eine Tendenz dazu, nicht inhärent sichere Maßnahmen oder Schutzmaßnahmen festzulegen, sondern Begleitmaterialien und Schulungsmaßnahmen als Maßnahmen für die Risikobeherrschung zu bestimmen. Dabei sollten Hersteller zwei weitere Fehler beim Risikomanagement vermeiden:
- Alle Maßnahmen, auch diese, müssen die Hersteller verifizieren – in diesem Fall durch eine summative Evaluation.
- Es gibt Informationen, welche nicht als risikominimierende Maßnahmen verwendet werden dürfen.
Weiterführende Informationen
Unter dem Schlagwort zu den risikominierenden Maßnahmen finden Sie Hinweise, welche Informationen zur Risikobeherrschung genutzt werden dürfen.
7. Fehlerklasse: Formale Fehler
Der siebte und letzte Typ an Fehlern beim Risikomanagement betrifft die formellen Anforderungen, welche Hersteller nicht erfüllen:
- Sie versäumen es, Dokumente in der Risikomanagementakte zu prüfen und freizugeben.
- Es fehlen Vorgaben (z.B. in Form einer SOP), die genau dies fordern.
- Der Zeitpunkt der Erstellung und Freigaben ist unlogisch. Beispielsweise wir die Risikomanagementakte freigegeben, obwohl danach noch Änderungen am Produkt erfolgen.
- Es lässt sich nicht mehr aufzeigen, auf welche Version des Produkts sich welche Version der Dokumente beziehen, weil beide, die Produkte und Dokumente, kontinuierlich weiterentwickelt werden.
- Es fehlen notwendige Dokumente in der Risikomanagementakte wie der Risikomanagementplan oder der Risikomanagementbericht.
- Den Dokumenten fehlen notwendige Inhalte z.B. zur Dokumentenlenkung (wie Autor, Version, Datum, Status) oder für die Konformität. Beispielsweise fehlt im Bericht die Aussage, ob die Risiken angesichts des Nutzens akzeptabel sind.
Fazit und Zusammenfassung
Keiner der Schritte beim Risikomanagement ist einfach:
- Festlegen einer Risikopolitik und von Risikoakzeptanzkriterien
- Erstellen eines Risikomanagementplans
- Identifizieren der Gefährdungen
- Bewerten der Risiken
- Festlegen und Verifizieren der Maßnahmen
- Verfassen des Risikomanagementberichts
Dennoch lassen sich die typischen Fehler beim Risikomanagement vermeiden. Dabei helfen:
- Die in diesem und den verlinkten Artikel genannten Tipps
- Ein interdisziplinäres und kompetentes Risikomanagement-Team
- Ein Management, das die Bedeutung des Risikomanagements versteht und diesem Team die notwendigen Ressourcen bereitstellt
- Das Seminar „Risikomanagement und ISO 14971“, das nicht nur einen schnellen Einstieg in das Thema verschafft, sondern bei dem auch die Tätigkeiten geübt werden
Das Johner Institut unterstützt Hersteller nicht nur beim Erstellen und Prüfen der ganzen Risikomanagementakte und dem Festlegen eines schlanken und konformen Risikomanagementprozesses.